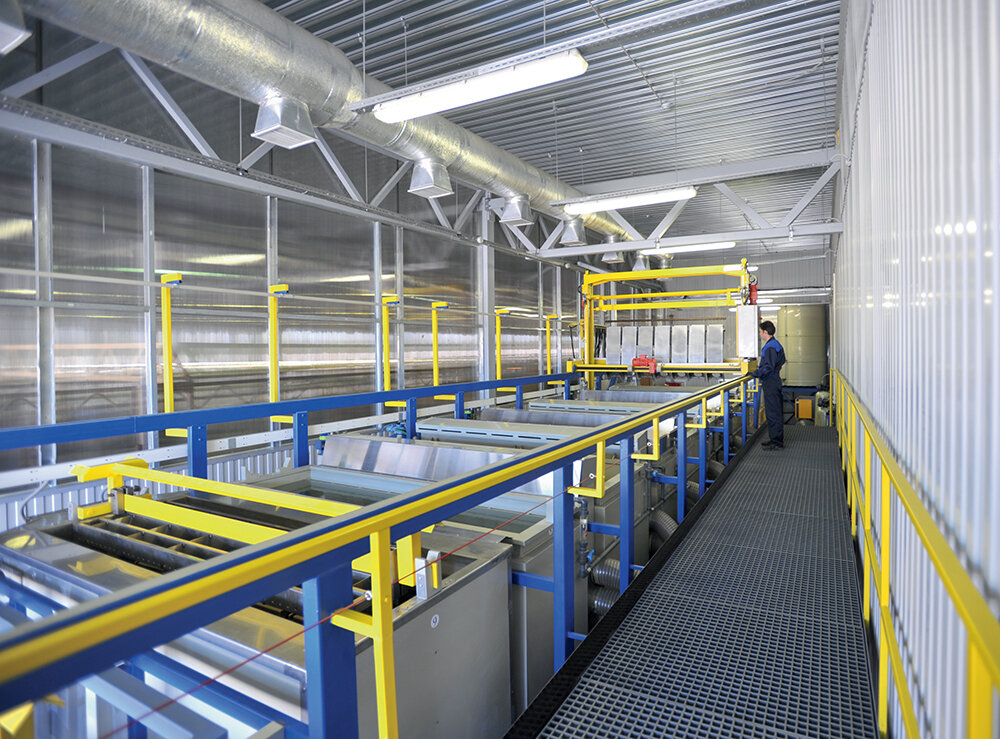
To protect against atmospheric corrosion and improve aesthetic design, the products are painted with powder coating, which is environmentally friendly and allows getting a perfectly even and durable coating. To get a high-quality coating, three components are important: the coating quality, the quality of the surface treatment, and the observance of polymerization technology.
The powder coating qualityPERCo uses Swiss architectural powder coatings of the IPG company. Such coatings are intended for long-term outdoor use, have increased resistance to light and weather, and allow getting an impact-resistant coating with the effect of pearl mica gloss and good elasticity.
Surface treatmentThe process of preparing products for powder coating is carried out on a special chemical preparation line. PERCo organized a laboratory, where for a whole year, the company was testing technologies of market leaders to select a surface treatment technology. As a result, the Henkel technology and products were chosen, which allow treating surfaces of products from both ferrous and aluminum alloys on the same line. To create a conversion layer, the Bonderite MNT-1 coating is used, which makes it possible to get a coating with a thickness of 50 nm (0.05 microns).
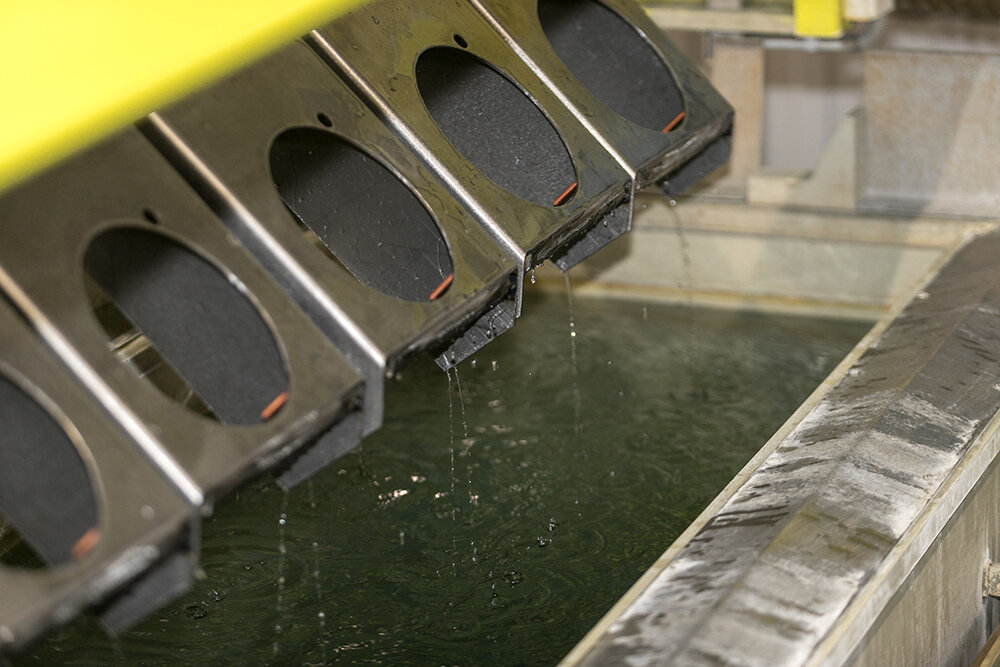
The line operates automatically, which minimizes disruption to the technological process. The chemical solution composition and washing water purity are analyzed daily. Steel parts go through 6 processing stages before drying, with 9 stages for aluminum parts.
Aluminum parts require more careful treatment due to the hard oxide film on the surface, which must be completely removed. If this is not done, the coating will have poor adhesion and will peel off over time. There is an aluminum clarification bath on the line, in which the oxide film dissolves, then the product is washed from the acid.
The powder coatingAfter the treatment, the parts are directly covered with paint. A powder polymer-based coating is applied to the surface. The coating is carried out by spraying a fine powder. Electrostatic charge of its particles attracts the powder to the surface of the painted parts. Then, the parts enter a curing oven where the powder layer is melted at a temperature of about 180 C and becomes density.
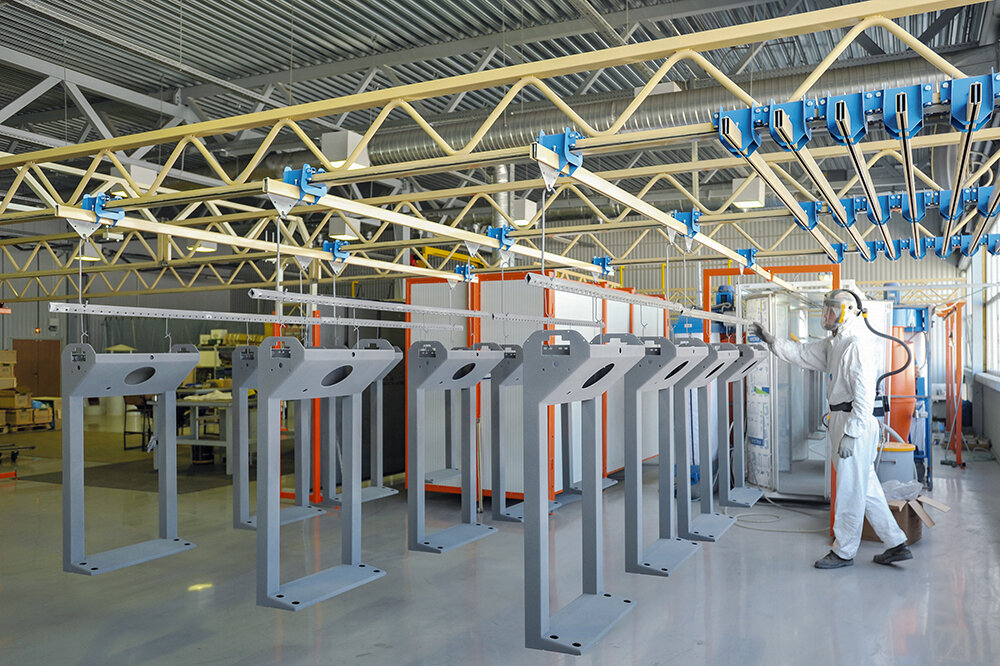
The powder coated samples of PERCo products have passed all tests carried out for 750 hours in a salt spray chamber according to the ISO 9227 test procedure of the Henkel laboratory. According to the test results, the corrosion category corresponds to C3, while the service life of the coating is estimated as high - over 15 years in a moderately polluted urban and industrial atmosphere in the open air.
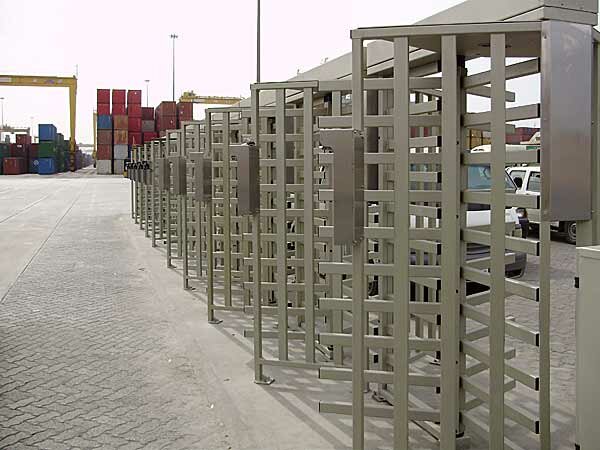
The high quality of the PERCo products' coating is confirmed by the long-term operation in various climatic conditions: in the seaports of Trieste, Dubai, Tallinn, at the Spartak stadiums in Moscow and Fisht stadiums in Sochi, Sokolniki Park, and many other facilities.